
So we noticed that without datum, there are high chances that a part may get rejected. The same goes true if the left side surface is important and the supplier measures the part like “Scenario-2.” But if the supplier measures the part like” Scenario-1″, then the part will not get assembled and will be rejected. Let us assume that the bottom surface is important for mating with other part and need to be flat. Now the manufacturer can measure those surfaces in two different ways, as shown on the right side. In the example, the left side image shows a typical dimension of a block. To understand why datum is required, we need to look into the below image. See this below example where all the hole positions are referenced from a datum named “ A“ Datum needs to be chosen carefully because choosing the wrong datum may cause the part to get rejected considering form, fit, and function. So datum acts as a reference point or an anchor for almost all geometrical tolerances and dimensions. So in this article, we will learn more about ” What is a datum in GD & T with definition, type, uses, and examples.īefore going ahead into this article, you can consider reading through the below list of articles as this will make things easy for you to understand datum in a better way.īasic GD & T rules as per ASME standard What Is A Datum: Datum definitionĭatum is a theoretical exact plane, axis, or point that GD & T or geometrical tolerances use to reference dimensions. Except for form tolerances like Straightness, Flatness, Circularity, and Cylindricity, all other geometrical tolerancing can refer to a datum to explain the design intent. Parallelism should never reference three datums, and this is because parallelism only controls orientation, not location.Datum plays an important role in GD & T.

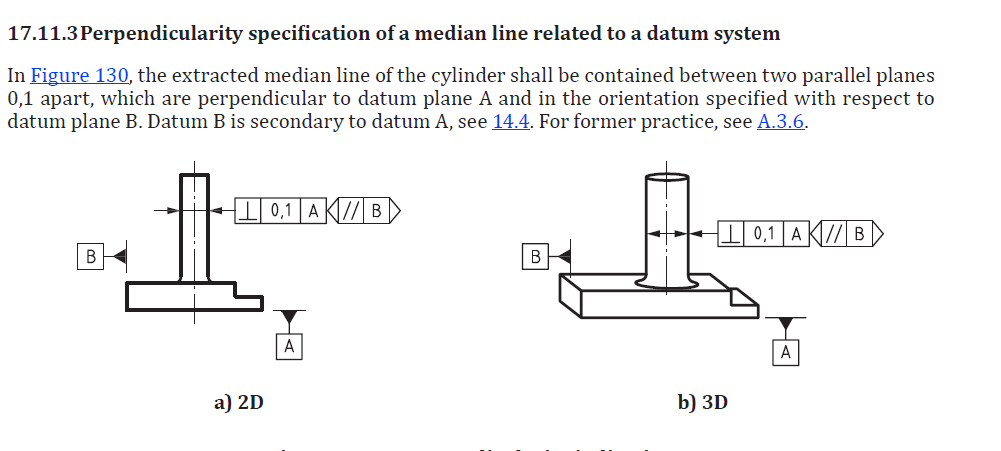
To summarize, the parallelism callout is used with one or two datum references, depending on the type of feature to be controlled. The axis cannot be parallel to the third datum plane, and it is, in fact, perpendicular. Now, the axis cannot rotate, and the orientation is fully constrained. If we want to lock down the orientation of the axis fully, we must add a reference to a second datum plane, C. Note that the axis can still be rotated in a plane parallel to datum plane B. Now, imagine that the hole axis must be parallel to one of these planes, B. Visualize three mutually perpendicular datum planes A, B, and C located along the coordinate system X, Y, and Z axes. However, we are not controlling size or location with this constraint, only orientation. The diameter symbol in this feature control frame indicates that the tolerance applies to a feature of size. The feature control frame for this callout will contain the parallelism symbol, a diameter symbol followed by the tolerance amount, and two datum plane references. Going back to our parallel surface example, we can allow the surface to be translated parallel to the datum plane or rotated about an axis perpendicular to the datum plane and still accurately define the desired parallelism tolerance zone.Ĭonsider a second example, where the orientation of a hole is controlled with a parallelism constraint. Parallelism controls the orientation of a feature, but it does not control location. Any additional datum planes referenced would not be parallel to plane “A” and would only serve to confuse the reader.Ī single datum plane reference is sufficient for a parallelism constraint for a surface because parallelism does not require us to constrain all six degrees of freedom. The parallel planes that form the tolerance zone boundaries are also perfectly parallel to datum plane “A.” As you can see, datum plane “A” provides all the information we need to define the parallelism constraint. For example, think of one surface of a part, and impose a parallelism constraint of 0.030, with respect to a datum plane “A.” The tolerance zone in this example is defined by two parallel planes 30 microns apart.
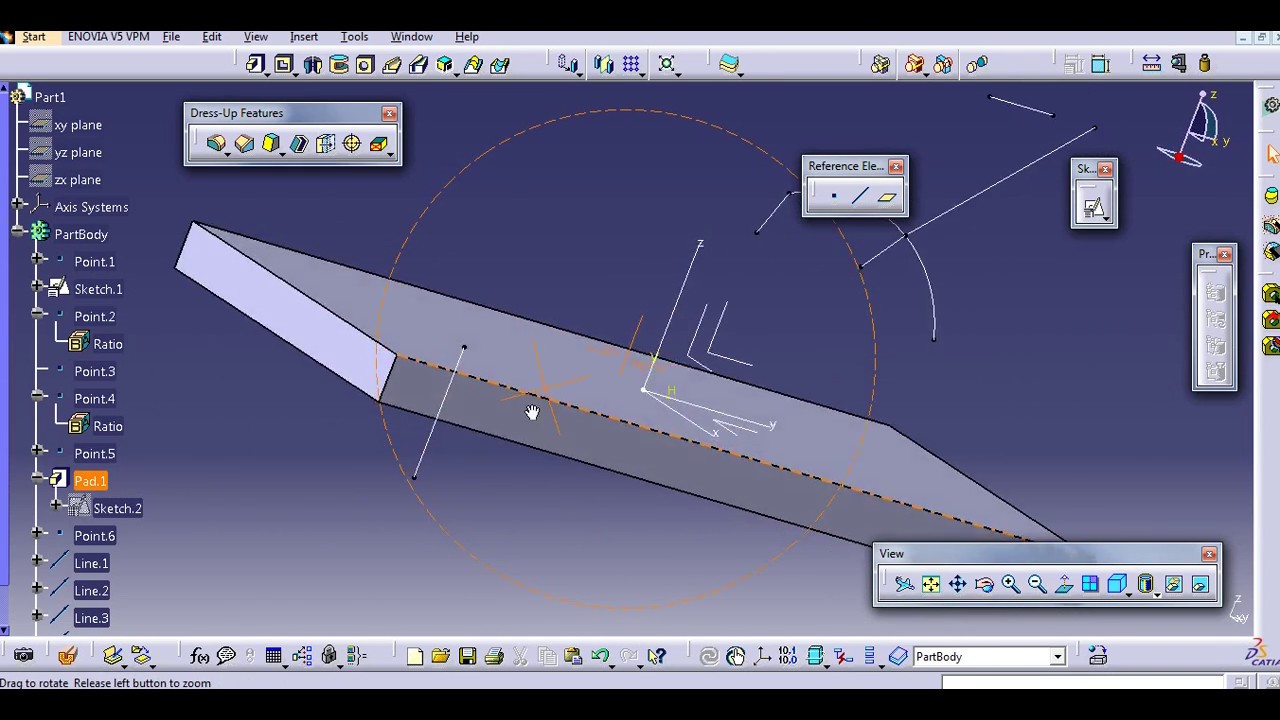
The feature control frame for this callout will contain the parallelism symbol, the tolerance amount, and a single datum plane reference. To explore this in more detail, we will first consider the parallelism of a surface.
